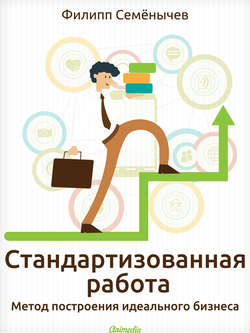
000
ОтложитьЧитал
1. От автора

Мечта построить идеальный бизнес хотя бы раз посещала любого руководителя вне зависимости от сферы его деятельности. Для одних идеальный – это самоуправляемый, а для других стабильный, приносящий определённую прибыль бизнес. Путей построения такого бизнеса можно предложить огромное количество, и в каждом случае они будут друг от друга отличаться. В настоящей книге описан один из наиболее сложных методов Бережливого производства (далее lean) под названием «Стандартизованная работа». Отличие этого метода от остальных методов и инструментов lean заключается в системном принципе его работы. Используя метод стандартизованной работы, вы не сможете применить его один раз, что-то улучшить и забыть о нём. Стандартизованная работа должна будет стать частью производственной или операционной системы вашей организации. Этот метод базируется на постоянном снижении потерь и непрерывном совершенствовании, что является необходимым направлением приложения усилий, с точки зрения lean, для построения идеального бизнеса.
Книга состоит из двух частей, в первой из которых акцент делается на культурных преобразованиях и подготовке к внедрению самого метода – организации решения проблем и совершенствования. Изучить первую часть рекомендуется всем руководителям и специалистам, начинающим или уже внедряющим принципы, методы и инструменты lean в повседневной деятельности. Вторая часть описывает непосредственно все составляющие метода и методику его внедрения. Она рассчитана на руководителей и специалистов, уже имеющих некоторый опыт применения инструментов и методов lean, например, активно внедряющих 5С[1] на рабочих местах или осваивающих методы картирования потока создания ценности[2].
Существует множество интерпретаций описываемого в настоящей книге метода, не говоря уже о нюансах, связанных со спецификой каждой организации. Сразу отмечу, что в настоящей книге изложена общая концепция, обобщающая лучший опыт применения метода. Множество предприятий и организаций по всему миру успешно его используют, улучшают свои процессы[3] и получают стабильные результаты. Некоторые примеры можно встретить и в нашей стране, хотя, по моему личному мнению, готовность к применению методов lean подобного уровня сложности в настоящее время крайне низкая. Тем не менее, несмотря на огромное множество проблем, связанных с низким уровнем знаний в этой области, а также укоренившимися с советских времён принципами работы, Бережливое производство (lean) продолжает развиваться. Я верю, что вскоре его развитие приобретёт государственную поддержку, сделав тем самым огромный шаг к повышению конкурентоспособности страны в целом.
Но пока этого не произошло, первые шаги следует сделать нам, тем, кто готов меняться и менять, улучшаться и улучшать, кто не боится экспериментировать и пробовать что-то новое. Я желаю вам с удовольствием реализовывать изменения и постоянно совершенствоваться, а также успехов в освоении принципов, методов и инструментов lean в вашей работе.
2. Введение

С тех далёких времён, когда обезьяна взяла в руку палку, можно дать старт отсчёту с момента начала поиска наиболее эффективного способа выполнения работы. Кому-то надо было быстрее и безопаснее убить зверя, кому-то надёжнее построить дом, а кому-то быстрее вспахать поле. В зависимости от вида работы в разные периоды развития человечества применялись различные методы и инструменты для повышения её эффективности. Под эффективностью в данном случае и далее по тексту мы будем понимать выполнение какой-либо деятельности с максимально возможным результатом и минимально возможными затраченными ресурсами. Не подлежит сомнению тот факт, что в ходе своего развития человечество постоянно искало пути выполнения любого рода деятельности наиболее быстрым, простым, надёжным и безопасным способом. Сначала человек использовал палку, потом стал применять эффект «рычага» для перемещения тяжёлых и крупных предметов. Прошло время, и люди стали добывать металлы и использовать их для изготовлений разного рода инструментов, стараясь изготовить их надежнее и удобнее. Этот процесс продолжается до сегодняшнего дня. Так, однажды, человек осознал, что разделение труда, т. е. выполнение отдельных его видов разными людьми, более производительно и требует меньше времени на подготовку работника, чем прежние способы. Концепция разделения труда впервые была описана Адамом Смитом[4] в первых трёх главах пятитомного трактата «Исследование о природе и причинах богатства народов». Параллельно с совершенствованием инструмента и оборудования шло совершенствование способов и методов производства.
На разных этапах развития человек считал наиболее эффективными определённые методы и способы работы. В качестве примера из истории можно привести первое появление непрерывного производства, автоматизированное изготовление изделий, появление первых конвейеров, которые в США использовались для разделки мяса. Несомненный вклад в развитие методов производства в начале прошлого века внёс Генри Форд[5], предложив унификацию деталей и внедрив концепцию «массового производства». «Массовое производство» как один из методов работы до конца прошлого века считался наиболее эффективным, пока «Тойота» на своём примере не доказала, что единичное производство всё же эффективней. Кто знает, что будет в рейтинге эффективности на первом месте завтра?
Если сначала совершенствование было обусловлено вопросами физического выживания человека, то в настоящее время вопрос стоит об экономическом выживании организованных групп людей, организаций. Благодаря достаточно развитым современным технологиям и развитию рыночной экономики, постоянно возрастают как потребности рынка, так и возможности их удовлетворения. В обстановке жёсткой конкуренции, организация, не работающая в направлении своего развития и не улучшающая свои процессы, методы и персонал, обречена на банкротство, либо жалкое бесприбыльное существование. Теперь от совершенствования методов работы зависит сам факт существования организации.
Поиски наиболее эффективного метода работы продолжаются до сих пор, это бесконечный процесс, обусловленный естественными законами эволюции. Появление и развитие lean технологий помогает в поисках и совершенствованиях различных методов и подходов, привнося всё новые идеи, накапливая и распространяя лучший опыт по всему миру.
Lean, в свою очередь, тоже метод – метод непрерывного совершенствования, выстроенный на принципах, наиболее эффективно работающих в современном мире, постоянно эволюционирующий, метод, в котором очень ценится новый опыт и предлагаются новые решения.
Причиной этого является необходимость постоянного совершенствования, обусловленная постоянным увеличением конкуренции.
Если вы встречались с понятием «lean» или активно внедряли некоторые принципы, методы или инструменты, вы знаете, что lean предполагает устранение потерь и непрерывные улучшения, которые начинаются не в офисе генерального директора организации, а непосредственно на рабочем месте, где создаётся ценность. Ценность – это то, за что готов платить Заказчик (действия, свойства, качество и т. п.). Таким образом, с точки зрения lean, наиболее эффективный метод выполнения работы должен быть сосредоточен именно на создании ценности для Заказчика.
В настоящей книге приводится концепция одного из наиболее эффективных методов работы, зарекомендовавших себя в последние десятилетия, метода работы на основе стандартов. Также в настоящей книге вы встретите примеры и опыт применения тех инструментов lean, которые необходимы для правильного функционирования этого метода.
Ниже в нескольких разделах подробно описывается метод работы на основе стандартов и даётся детализованное объяснение такого сложного метода lean, как «стандартизованная работа» (standard work). Весь известный опыт применения этого метода мировыми организациями, а также передовыми российскими компаниями максимально сосредоточен в описании нюансов изложенных методик. В переводе с английского «лучший опыт» (Best practices) ещё означает лучший результат, достигнутый определённым, отличным от остальных, способом, который используется в качестве ориентира для дальнейших улучшений. Запомните это определение, мы к нему ещё вернёмся.
Сформулировать проблему, которую предлагается решить в настоящей книге, можно так: «необходимость постоянного совершенствования», сколько бы ни существовало различных причин для этого. Такая формулировка остаётся актуальной на протяжении многих десятилетий и останется таковой ещё долго.
Так какой же должен быть идеальный метод работы в представлении современного человека? Представьте, что некто пришёл на новую работу, где после краткого инструктажа по пути на рабочее место он начинает выполнять такие же операции, с тем же качеством и скоростью, как и уже работающие сотрудники. Продукция выпускается только в нужном количестве и необходимого качества, а все показатели того и другого известны каждому работнику. Естественно, работа постоянно улучшается: вводятся новые инструменты и оснастка, улучшается эргономика на рабочих местах, сокращаются бесполезные действия, в чём заинтересованы и активно принимают участие как руководители, так и сами рабочие. Думаете, звучит не очень реалистично? Тем не менее, так работает не только знаменитая благодаря своей производственной системе компания Toyota, но и множество других компаний по всему миру.
Преимущества такой ситуации очевидны. Работника не надо дополнительно обучать, затрачивая драгоценное время, ведь при возникновении вопросов находящийся рядом коллега всегда сможет на них ответить. Устранение потерь в работе не только ведёт к снижению затрат на изготовление продукции в составе его себестоимости, но и мотивирует работника на дальнейшие улучшения. Лучший опыт не теряется спустя некоторое время, а накапливается в постоянно совершенствующихся стандартах. Таким образом, мы снова приходим к двум основным признакам наиболее эффективного метода работы – постоянному устранению потерь и непрерывному совершенствованию.
Настоящая книга призвана помочь как руководителям, так и lean тренерам, практикующим внедрение отдельных принципов, методов и инструментов lean. То есть по умолчанию считается, что у читателя есть по крайней мере небольшое представление о том, что такое lean или Бережливое производство. Иначе его вряд ли бы заинтересовала эта книга. Однако для лучшего усвоения информации в ходе изложения приводятся пояснения некоторой lean терминологии, особо важная информация выделяется жирным шрифтом. Согласно lean-подходу автора, настоящая книга содержит только необходимую для освоения темы информацию: алгоритмы работы, описания и примеры реализации методов и инструментов. Поэтому в содержание книги сознательно не включались мотивирующие монологи и рассуждения «вокруг да около». В связи с этим, убедительная рекомендация (если хотите, просьба): останавливаться и прорабатывать каждый раздел, при необходимости возвращаясь к его содержанию. Наибольшую пользу настоящая книга принесёт при составлении плана работ, за основу которого можно взять приведённые далее алгоритмы работы, и немедленном применении описанных методов и инструментов, сразу после её прочтения.
Читателю, намеревающемуся применять описанные в настоящей книге методы и инструменты, сразу необходимо уяснить для себя, что применение различных инструментов и наполнение сопутствующей документации будет различаться в зависимости от специфики стандартизируемых процессов. Прежде чем продолжить чтение, забудьте такие словосочетания, как «это не применимо к нашей работе», «у нас особая специфика процессов» и прочие подобного рода. Изучайте суть методов и обращайте внимание на логическую последовательность работы описываемых методов и инструментов. Во время чтения старайтесь представить, как тот или иной метод применим к вашим процессам, как можно применить описанные инструменты в вашем производстве.
Материал в настоящей книге структурирован следующим образом (см. рисунок 2.1):

Рис. 2.1
В разделе 3 под названием «Снижение потерь» описывается то, что мы знаем о потерях, об их формах и видах, об их влиянии на предприятие в целом, а также рассказывается о взаимосвязи между потерями и проблемами. Даётся описание методам работы с проблемами и их причинами, отличительным особенностям самих проблем и причин, а также приёмам формирования lean мышления и lean взгляда на проблемы.
В разделе 4 «Непрерывное совершенствование» объясняется, чем принципиально отличается решение проблемы от совершенствования и что такое кайдзен. В этом разделе вы найдете описание принципов lean, направленных на выработку культуры непрерывного совершенствования, а также способов формирования необходимых привычек у персонала. Отсюда же вы узнаете об отличительных особенностях культуры непрерывного совершенствования и научитесь основным методам и способам построения в организации этой культуры (система подачи и реализация предложений, мотивация и информированность персонала, целеполагание и лидерство).
В разделе 5 «Стандарт и методы работы на основе стандартов» фокусируется внимание на роли стандарта с точки зрения lean, описываются основные требования, предъявляемые к стандарту, его функции и взаимосвязи между стандартами. Объясняются различные трактовки понятий стандарта и стандартизованной работы, разъясняется понимание методов работы на основе стандартов, описывается механизм работы этих методов.
В разделе 6 «Стандартизованная работа» подробно описываются условия реализации метода и необходимые для этого подготовительные работы. Также, подробно описывается содержание каждого документа, метода, их сочетаний, а также приводятся примеры их выполнения. Объясняется порядок работы метода.
В разделе 7 «Внедрение Стандартизованной работы» подробно разъясняется общий алгоритм внедрения метода, объединяющий в единое целое весь изложенный ранее материал. Дополнительно объясняются наиболее проблемные этапы внедрения, даются рекомендации по избеганию наиболее распространённых проблем и подготовки персонала к изменениям.
В разделе 8 «Дополнительные функции» рассказывается о применении метода для обеспечения качества выпускаемой продукции, приводится алгоритм встраивания качества в рассматриваемый процесс. Объясняются дополнительные элементы метода, обеспечивающие контроль его работы, помогающие в управлении персоналом, а также рассматривается применение метода в различных процессах, при разработке новой продукции. Подробно описываются направления для совершенствования при внедрении метода, которые посредством небольших улучшений помогают избавляться от потерь и совершенствовать процесс в целом.
3. Снижение потерь

Что мы знаем о ценности и потерях?
Вначале необходимо разобраться с понятием «потеря». Чтобы это сделать, надо понимать, что такое ценность как противоположное понятие. Как уже было сказано, ценность – это то, за что готов платить Заказчик (действия, качества, свойства продукта и т. п.)
Время создания ценности (ВСЦ) – промежуток времени, в течение которого продукт видоизменяется, либо приобретает свойства, интересующие Заказчика, т. е. приобретает ценность. Самый простой и наглядный пример из производства – это операция штамповки металлических заготовок на каком-либо прессе. Время цикла, затрачиваемое на штамповку одного изделия, может включать в себя время укладки листа, регулировки штампа, передвижение оператора на безопасное расстояние и т. п. Однако, время создания ценности – это только момент удара, когда из металлического листа появляется заготовка. Время создания ценности может составлять секунды или даже доли секунд. Заказчика интересует только тот момент времени, когда в листе металла происходит перегиб в нужную сторону под нужным углом. Но ему придётся платить за всё время производственного цикла, т. к. передвижения рабочих, поломка пресса и ожидание доставки металла уже включены в стоимость продукта.
Потерями, с точки зрения lean, считаются все действия, потребляющие ресурсы, но не создающие ценности. Другими словами, потери – это действия, не видоизменяющие продукт в необходимую для Заказчика сторону и не придающие ему необходимых Заказчику свойств.
Зачем устранять потери?
Устранение потерь является неотъемлемой частью совершенствования как организации в целом, так и определённого, создающего ценность, процесса. Почему же устранение потерь так важно? Мы не просто так останавливаемся на этом подробней.
Прибыль, получаемая организацией от реализации продукта или услуги, является разностью стоимости и себестоимости товара (услуги).
Прибыль = Стоимость – Себестоимость
В современном мире стоимость продукта определяется тем, сколько определённый сегмент рынка готов заплатить за продукт, учитывая его качество и сроки изготовления. Как правило, в сфере продаж на любой товар устанавливается максимально возможная стоимость, за которую только можно его продать. В свою очередь, стоимость сильно ограничена давлением рынка, т. е. конкуренцией, не позволяющей поднимать цены выше определённого уровня, что является частью современной рыночной экономики. Со стоимостью всё просто.
В lean нас интересует как раз себестоимость, т. е. издержки, которые несёт организация при изготовлении определённого продукта или оказании определённой услуги, т. е. средства, необходимые для нормального поддержания производства продукции и существования организации. Это затраты на сырьё и материалы, заработную плату работников, электроэнергию и прочие ресурсы. Говоря lean языком, себестоимость состоит из издержек на создание ценности для Заказчика и бесполезных издержек, т. е. потерь.
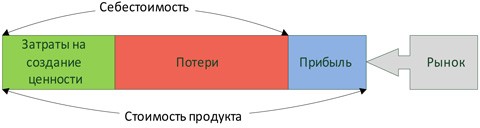
Рис. 3.1
Сокращая потери, мы уменьшаем соответствующие издержки и себестоимость изделия (см. рисунок 3.1). Далее простая арифметика: при неизменной стоимости снижение себестоимости приводит к увеличению прибыли. Если в масштабах организации всё понятно, то в масштабах цеха, участка или отдела снижение потерь может выражаться через уменьшение бесполезной работы (перемещений, транспортировки, невостребованных действий и т. п.), т. е. трудоёмкости, при сохранении фонда оплаты труда в коллективе. А может выглядеть в виде определённых локальных улучшений, улучшении эргономики на рабочем месте, таких как сокращение перемещений или сокращение бесполезной бумажной работы, и т. п.
В настоящее время в большинстве продвинутых компаний принято измерять работу человека и состояние процесса определёнными показателями, отражающими их эффективность и результативность. Снижение потерь, несомненно, сказывается на этих показателях. Более того, снижение потерь само по себе должно подлежать измерению. Как мы можем утверждать, что снизили потери, если мы не знаем, сколько их было и сколько стало? Другими словами, если мы сокращаем передвижения работника, мы должны понимать, на сколько метров сокращено перемещение, и сколько времени высвобождено в результате, как это отражается в общей картине выполнения работ, например, в масштабе участка или цеха. Стоит обратить внимание на то, что большинство потерь, устраняемых в отношении работника, удобнее измерять в единицах измерения времени (секундах, минутах, часах). Желаемый результат устранения потерь в масштабе организации лучше измерять уменьшением фактических затрат рабочего времени, увеличением производительности труда и повышением качества изделия.
Само по себе устранение потерь, например, на рабочих местах, ведёт к улучшению общих показателей организации, которые направлены на достижение максимальной прибыли, для чего и работает организация.
Например, сокращение перемещений рабочего в количестве 150 метров за цикл его работы (постоянно повторяемую последовательность действий) или времени, затрачиваемого на изготовление одного изделия, которое может составить, например, 100 секунд. При 10 циклах в смену это уже составит 1000 секунд, а в месяц – 22000 секунд или 6,1 часа, т. е. почти одну лишнюю рабочую смену. А это уже намного значительнее, чем просто 150 метров.
Можно сделать вывод, что выявление и устранение потерь означает постоянный рост благосостояния организации в целом и каждого её работника в частности. Отдельно говорить о необходимости выявления и устранения потерь нет смысла, так как она просто очевидна. Стоит отметить только одну важную аксиому – очень сложно увеличить уровень продаж, например на 10 %, но снизить издержки на 10 %, устраняя потери, достаточно просто, при этом потенциал для устранения потерь присутствует в каждом процессе, вне зависимости от его уровня совершенства. Другими словами, сколько бы раз вы не улучшали процесс (рабочую операцию, стандарт и т. п.), нельзя сказать, что больше улучшить ничего нельзя, потенциал есть всегда и везде, даже в самых высокоэффективных процессах. Устранение потерь – это всего лишь некие малые шаги в направлении достижения целей и процветания организации.
Таким образом, снижая потери, мы снижаем различного рода издержки, затрачиваемые на производство, следовательно, снижаем себестоимость продукта и тем самым высвобождаем средства и ресурсы для дальнейших улучшений.
Как выглядят потери?
Для того чтобы устранять потери, их необходимо знать в лицо. Другими словами, нужно уметь их определять, отличать друг от друга, понимать и оценивать негативное воздействие.
Поскольку сам инструмент «Стандартизованная работа», о котором идёт речь в настоящей книге, призван минимизировать потери при выполнении операций на уровне действий работника, необходимо чётко понимать, что из себя собой представляют основные потери, на что они влияют и как их можно распознать.
Различают семь видов потерь:
Перепроизводство, т. е. производство объёмов продукции, превышающих необходимое их количество. Любой может вспомнить примеры из своей памяти, когда в погоне за производительностью руководители забывали, что количество продукта, который готовы купить потребители, определяется рыночным спросом. В результате гонки за количеством происходит накопление больших объёмов незавершённого производства на производственных стадиях, появляются незаметные на первый взгляд дополнительные расходы на хранение, происходит избыточное использование материалов и ресурсов, нарушается график поставок изделий и комплектующих и т. д. Как следствие, можно наблюдать увеличение тех самых издержек производства в составе себестоимости изделия. Перепроизводство считается наиболее вредоносной потерей, так как оно влечёт за собой появление остальных видов потерь: ожидание – как правило, взаимообратная сторона производства; излишние запасы – прямое следствие перепроизводства; транспортировка и перемещение, связанные с наличием завышенного количества запасов; дефекты, количество которых имеет прямую зависимость от количества запасов.
Транспортировка, т. е. перемещение материалов, изделий, комплектующих. Из определения понятия «ценность» можно сделать вывод, что любое перемещение является потерей. Любое производство представляет собой последовательность операций по преобразованию сырья или полуфабрикатов в конечный продукт, а между операциями все эти материалы и полуфабрикаты необходимо перемещать. Поэтому транспортировка является неотъемлемой частью производства, как правило, без неё не обойтись. Тем не менее, это затраты на горючее или электроэнергию, на обслуживание транспортного парка, на организацию транспортной инфраструктуры (дорог, гаражей, эстакад и т. п.). Это также риск повреждения продукции и увеличение времени производственного цикла. Другими словами, момент времени от поступления в процесс сырья до момента времени выхода годного изделия значительно увеличивается из-за этой потери.
Ожидание – простой и бездействие человека.
Наличие ожидания может быть вызвано тем, что процесс планирования и процесс производства либо не согласованы между собой, либо имеются серьёзные проблемы процесса (например, поломка оборудования). Другие причины – различная пропускная способность операций, планирование не для нужд потребителей, а для загрузки оборудования и прочие.
Стоит отметить, что ожидание – наименьшая по вредоносности потеря, так как когда человек ожидает и ничего не делает, он и навредить ничем не может: не сделает брак, не произведёт продукции больше необходимого количества и т. д. Поэтому на практике, один из способов борьбы с потерями является их перевод в потерю ожидания (ведь тем самым уменьшается их негативное воздействие). Наиболее наглядный пример с ожиданием – это остановка оператора в случаях выполнения плана или появления некачественных изделий.
Излишние запасы, как уже было сказано выше, являются следствием перепроизводства и влекут за собой появление таких потерь, как транспортировка, перемещения и дефекты. С точки зрения экономики, запасы – это замороженные деньги, т. е. деньги, заключённые в оборотных средствах организации, вложенные в закупку сырья, материалов, комплектующих, в зарплату работника предыдущих операций процесса и в прочие расходы по созданию добавленной стоимости, но не совершившие оборот и не высвободившиеся в виде реализованного готового изделия. Это деньги, застывшие в виде незавершённого производства на различных стадиях процесса изготовления того или иного изделия.
Дефекты и брак по-другому можно назвать выпуском продукции, несоответствующей требованиям Заказчика. Следствие этой потери – затраты сырья, материалов и рабочего времени на доработку, либо затраты на переработку и утилизацию брака. Необходимо помнить, что кроме того, что брак нужно произвести, его надо обнаружить, идентифицировать как таковой, т. е. провести контроль изготовленной продукции, а затем либо дорабатывать, либо утилизировать, на что затрачиваются все вышеперечисленные ресурсы.
Одна из особенностей взаимозависимости потерь заключается в том, что по мере повышения уровня незавершённого производства в процессе, уровень дефектной продукции тоже увеличивается. Это объясняется не просто математическим наличием доли дефектных изделий в определённом объёме продукции, но и некоторыми психологическими аспектами человеческого восприятия производства. Человек устроен так, что в большей массе незавершённого производства несколько бракованных изделий ему будут не заметны (как капля в море). Поэтому, имея перед собой большие заделы, человек может даже бессознательно пропускать изделия, которые при отсутствии заделов, вызвали бы у него сомнения, либо были бы отбракованы. Ответственность человека, пропускающего дефект в массе незавершённого производства, будто растворяется в ней.
Излишняя обработка – видоизменение изделия, придание ему свойств или качеств, в которых не нуждается Заказчик, т. е. тех, которые не представляют для него ценность. Пример излишней обработки: изготовление продукции лучшей, чем того требуют клиенты, добавление ненужных функций или этапов производства, которые маскируют дефекты, а также доведение продукта до состояния, требуемого потребителем. Например, упаковывание изделия в более дорогую, требующую большей трудоёмкости, упаковку, либо ручная доработка стандартного изделия под требование Заказчика (разумеется, если за доработку не заплачены дополнительные деньги, компенсирующие соответствующие издержки).
Перемещения наряду с транспортировкой являются потерей по определению. Когда работник ходит, ценности он не создаёт (разумеется, если мы не рассматриваем работу курьера). Перемещения – излишние переходы человека, движения, настройки при выполнении работы, которые могут быть вызваны либо отсутствием и некорректностью стандартов выполнения работы или низким уровнем трудовой дисциплины и организации рабочих мест.
Как заметить потери?
Работая с потерями, необходимо понимать, что потери – это действия, не добавляющие продукту (услуге) ценности. Порой бывает достаточно просто выявить один или несколько видов потерь, согласно принятой классификации, одна из функций которой заключается как раз в упрощении поиска и идентификации потерь. Однако часто процессы бывают настолько запутанными, что выявить не только все, но и какую-либо часть потерь бывает достаточно сложно. В первую очередь необходимо концентрироваться на том, в чём состоит ценность. Из своего опыта могу отметить, что выделять ценность в любом процессе гораздо сложнее, чем искать потери. Сконцентрировавшись на том, что создаёт ценность в процессе, определив её, всё остальное можно идентифицировать как потери. Напрашивается вполне логичный вопрос: для чего тогда вообще необходима классификация потерь? Если внимательно изучить все потери какого-либо одного процесса, то можно понять, что между ними существует тесная взаимосвязь: одни потери являются следствиями других и причинами третьих, устранение потерь в одной зоне может как увеличить, так и уменьшить потери в других (например, в соседних) зонах. Вышеприведенная классификация помогает не только быстрее выявлять потери, но и понимать их взаимосвязь и концентрироваться на наиболее значимых из них. Здесь мы подходим к вопросу расстановки приоритетов, на котором подробнее остановимся далее. Пока приведём несложный пример из производственной сферы – изготовление маленького литого заборчика, который можно встретить на улицах, в скверах и парках. Процесс его изготовления состоит из множества различных операций, большинство из которых сами по себе являются недобавляющими ценности, их мы отбросим сразу. Если перечислять по порядку, в зависимости от технологии и применяемой терминологии, операции можно расположить следующим образом: подготовка шихты[6], плавка металла, изготовление формы, заливка металла, выбивка отливки из формы, обрубка, очистка. Начинаем думать, что же в этом процессе интересует Заказчика? За что он готов платить деньги? Давайте поставим себя на его место. В первую очередь ему необходим качественный заборчик, поставленный ему в определённый срок по оговоренной цене. Вспоминаем, что во время создания ценности происходит видоизменение продукта, он приобретает необходимые для Заказчика качества и свойства. Таким образом, получаем, что в первую очередь создаёт ценность операция плавки, т. к. она придаёт металлу, из которого состоит заборчик, необходимые качества и свойства. Изготовление формы также составляет ценность для заказчика, т. к. придаёт изделию необходимую конфигурацию. Создающие ценность заливка металла, обрубка и очистка являются теми необходимыми операциями, которые видоизменяют изделие. Получается, что мы уже отбросили подготовку шихты и выбивку отливки из формы. В данном примере мы не берём во внимание множество сопутствующих операций, которые могут существовать в этом процессе, таких как различные загрузки, завешивания и транспортировки, так как они не создают ценности в принципе. Продолжая анализ дальше, мы рассматриваем каждую операцию, подробней разбирая её составляющие. Например, в чём именно заключается ценность в операции заливки металла? Время, когда струя расплавленного металла необходимого химического состава заполняет форму, попадая в литниковую чашу[7] и растекаясь, образуют конфигурацию отливки заборчика, это время, добавляющее ценность. Остальные действия, начиная с подготовки заливочного ковша, транспортировки металла и даже наклона заливочного ковша, до момента, когда струя металла попала в чашу, и все прочие, не добавляют ценности, в это время изделие не видоизменяется, не преобразуется и не приобретает необходимые качества и свойства.