Контроль качества изготовления и технология ремонта композитных конструкций
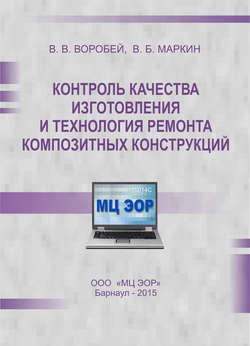
000
ОтложитьЧитал
Введение
Среди наиболее важных требований, предъявляемых к конструкциям современных летательных аппаратов (ЛА) и ракетно-космической техники, можно назвать минимальную массу, максимальную жесткость и прочность, максимальный ресурс работы конструкций в условиях эксплуатации, высокую надежность. В значительной мере перечисленные требования обеспечиваются выбором материала и совершенством технологии изготовления конструкции из данного материала.
Комплексу перечисленных требований больше всего удовлетворяют композиционные материалы (композиты) на основе современных углеродных, борных, органических и стеклянных волокон в сочетании с полимерными, металлическими, углеродными, керамическими и другими видами матриц.
При изготовлении конструкций из композиционного материала (КМ) совершенство технологии определяется выбором оптимальных параметров технологического процесса, техническим уровнем используемого оборудования и оснастки, наличием надежных методов неразрушающего контроля как самой конструкции, так и полуфабрикатов для их производства. В настоящее время технология производства элементов ЛА из КМ развивается опережающими темпами практически во всех промышленно развитых странах. Надежность любой конструкции определяется правильным выбором проектных данных и стабильностью технологических параметров в процессе изготовления, достаточностью контрольных операций и возможностью ремонта в процессе контроля изделий. Конструкции из КМ, нашедшие широкое применение в аэрокосмической технике и машиностроении (рисунок 1, 2), поставили перед разработчиками современных технологий многочисленные проблемы, связанные с сокращением производственно-экономических потерь в процессе их изготовления и эксплуатации.
Несовершенство технологического оборудования, используемого для получения исходных компонентов КМ (нитей, лент, тканей, особенно углеродных), а также для переработки их в изделие, низкий уровень автоматизации этого оборудования, разброс параметров технологического процесса получения композиционных материалов, недостаточный контроль параметров технологического процесса при получении препрегов, формировании пакета КМ, термообработке, механической обработке, приводят к возникновению различного рода производственных дефектов, снижающих несущую способность и работоспособность разрабатываемых конструкций. Особенность композитов, как известно, в том, что они не являются материалом в классическом смысле этого слова, таким как, например, металлы, фактически это – конструкция, создаваемая в процессе изготовления изделия. При этом композиты, выполненные из одного и того же наполнителя (волокна) и связующего по одинаковой технологии, могут иметь различные физико-механические характеристики, которые способны изменяться в широком диапазоне за счет выбора числа направлений армирования и объемных долей волокна в каждом направлении армирования.
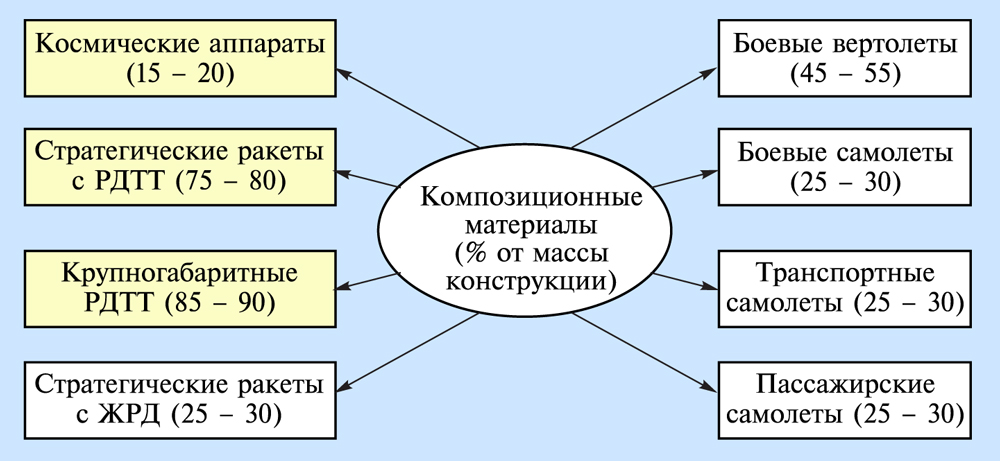
Рисунок В.1 – Применение композитов в ракетной и аэрокосмической технике:
РДТТ – ракетный двигатель твердого топлива; ЖРД – жидкое ракетное топливо
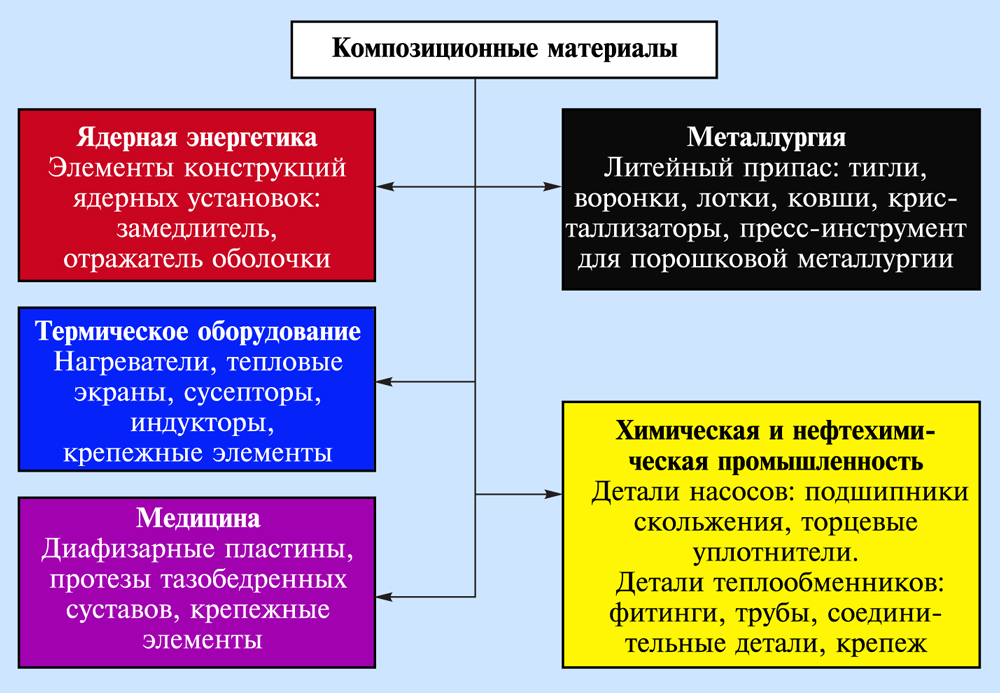
Рисунок В.2 – Применение углерод-углеродных композиционных материалов в различных областях народного хозяйства [5]
Важнейшее достоинство композитов – возможность создавать из них элементы конструкций с заранее заданными свойствами, наиболее полно отвечающими характеру и условиям работы. Многообразие волокон и матричных материалов, различных схем армирования, используемых при создании композитов, позволяет направленно регулировать прочность, жесткость, уровень рабочих температур и другие свойства путем подбора состава, соотношения компонентов и макроструктуры компонента.
При изготовлении композиционных материалов и конструкций из них важнейшее место занимают процессы формирования силовой основы – каркаса композита, структура которого определяется направлением действия главных напряжений для каждой конкретной конструкции и типом применяемого материала.
В современных конструкциях используются каркасы, образованные из слоев, армированных параллельными непрерывными волокнами, с хаотическим и пространственным армированием. Широко используются композиты, где структура каркаса образована пространственным плетением нитей и жгутов, и композиты со стержневым армированием (свойства их определяются свойствами стержней, изготовленных из прямолинейных нитей и жгутов). На рисунке В.3 представлены различные виды армирования каркасов в композиционных материалах. Например, волокнистое армирование позволяет использовать принципиально новые методы проектирования и изготовления изделий, основанные на том, что материал и изделие создаются одновременно в рамках одного и того же технологического процесса.
В результате совмещения армирующих элементов и матрицы образуется новый комплекс свойств композита, в том числе и свойства, которыми изолированные компоненты не обладают.
Появление ряда новых свойств связано с гетерогенной структурой, обусловливающей наличие границы раздела между волокнами и матрицей, в частности армирующими элементами и матрицей, существенно повышает трещиностойкость композита. Высокое сопротивление развитию разрушающих трещин в волокнистых материалах обусловлено их работоспособностью при значительных накопленных повреждениях.
Нестабильность технологических процессов изготовления конструкций из композиционных материалов, связанная с новизной и сложностью их реализации, ставит на первый план проблемы качества выпускаемой продукции. Обеспечение контроля качества всего объема выпускаемой продукции возможно только при условии применения методов и средств неразрушающего контроля (НК), который относится к числу наиболее приоритетных направлений научно-технического прогресса.
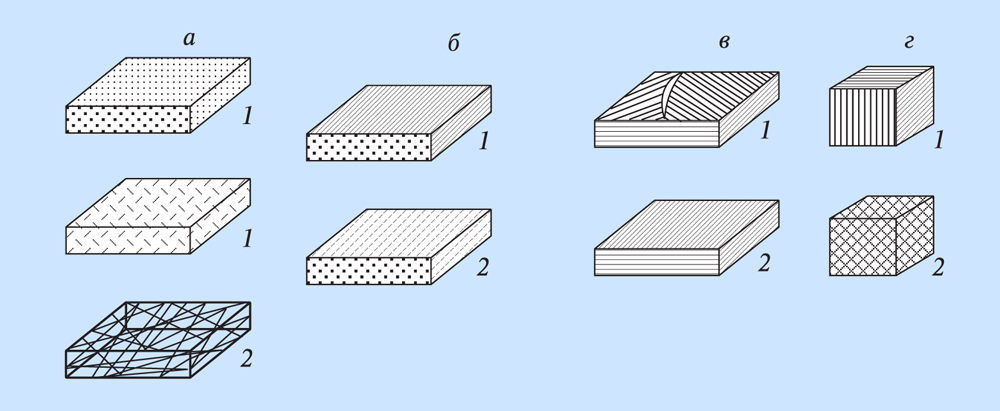
Рисунок В.3 – Классификация композитов по конструктивному признаку:
а – хаотически армированные: 1 – короткие волокна, 2 – непрерывные волокна; б – одномерно-армированные: 1 – однонаправленные непрерывные, 2 – однонаправленные короткие; в – двумерно-армированные: 1 – непрерывные нити, 2 – ткани; г – пространственно-армированные: 1 – три семейства нитей; 2 – n семейств нитей
Существует четыре наиболее важных направления развития неразрушающего контроля и диагностики: интеллектуализация методов и средств контроля и диагностики, разработка единой системы контроля качества технических объектов и окружающей среды, совершенствование диагностических технологий, организационное обеспечение неразрушающего контроля и диагностики на международном уровне [18].
В комплексе действий, направленных на обеспечение надежности и долговечности разрабатываемых конструкций из композиционных материалов, использование высокоэффективных методов неразрушающего контроля имеет решающее значение, поскольку малейшая ошибка в определении характера дефекта или его пропуск могут привести к труднопредсказуемым последствиям. Несмотря на существующие разнообразные методы и средства НК, до сих пор они не могут удовлетворять в отдельности потребности современного производства.
Анализ катастроф и их связи с конструкционными аспектами требует целенаправленной работы по изучению обстоятельств разрушений, их причин и сопутствующих факторов, выявлению определяющих процессов, оценке параметров и диапазонов их безопасных изменений. Исследования такого плана осуществляются с различных теоретических и концептуальных позиций с использованием различных информационных технологий. Изучается влияние особенностей конструктивного исполнения, технологии изготовления, характера нагрузок и воздействий. Большое внимание уделяется оценке эффективности применения высокопрочных материалов, методов неразрушающего контроля, различных ограничителей нагрузок, живучести конструкций в условиях аварий, проектируемых и запроектных, применяемых методов расчета прочности и ресурса. Обычно исследования этого направления базируются на традиционных методах строительной механики и теориях конструкционной прочности [15].
Особо рассматриваются вопросы механики, физики и химии деградационных процессов, приводящих в связи с необратимыми изменениями и повреждениями в структуре материалов к снижению прочностных характеристик, образованию и росту трещин, а также к катастрофическим отказам конструкций. Характер деградационных процессов и их роль в формировании разрушений существенно зависят от типа технической системы. Например, для баллонов давления и сосудов высокого давления основными причинами считаются механическая усталость, дефектность изготовления и коррозионные процессы в металлических фрагментах конструкции. Следовательно, дефектность конструкции и наличие трещин и расслоений остаются определяющими источниками разрушений.
Другой важной стороной обеспечения качества продукции является разработка и обоснование допустимости специализированных технологий ремонта создаваемых конструкций с учетом специфики структурных и технологических дефектов. Реализация этой проблемы обеспечивает значительное повышение выхода годной продукции в условиях дефицита исходных материалов и высокой стоимости конечной продукции.
В учебном пособии исследуются и разрабатываются вопросы, связанные с технологическими процессами контроля качества, изготовления и ремонта конструкций из композиционных материалов. Широкое применение конструкций из композитов потребовало разработки новых методов и аппаратуры неразрушающего контроля для осуществления непрерывного контроля непосредственно в процессе формирования композиционных материалов и изделий из них. Анализ существующих структурных дефектов в композиционных материалах и технологических дефектов в конструкциях позволяет разработать научно обоснованные технологии ремонта, обеспечивающие требуемую надежность создаваемых изделий.
Глава 1
Неразрушающий контроль параметров процесса изготовления конструкций из композиционных материалов
1.1 Требования, предъявляемые к методам контроля
Обеспечение высокого качества и надежности изделий из КМ невозможно без применения эффективных современных методов контроля на всех стадиях производственного цикла: проектирования (разработка), изготовления, эксплуатации. При этом каждой стадии соответствуют свои методы контроля. Наиболее эффективны неразрушающие физические методы контроля (НФМК) качества, применяемые на стадии как изготовления (обработки, исследования), так и эксплуатации изделий. Следует отметить, что наибольший эффект от НФМК достигается при применении его в мелко- и среднесерийном производстве крупногабаритных изделий, когда возможен сплошной контроль качества. В крупносерийном производстве более эффективны статистические методы выборочного контроля, при этом методы контроля качества подразделяются по количественным, качественным или альтернативным признакам.
К количественным методам контроля относят такие, которые позволяют регистрировать точные численные значения параметров, определяющих качество изделия. Качественные методы позволяют отметить лишь категории, классы (сортность, хорошее, плохое и т. д.), к которым принадлежит контролируемое изделие. В том случае, когда изделия подразделяются на годные или дефектные, осуществляют контроль по альтернативному признаку, что является частным случаем контроля по качественному признаку.
Определение соответствия изделия данным условиям (по размерам, физико-механическим свойствам, структуре материала, состоянию поверхности – шероховатости, наличию тех или иных дефектов и др.) осуществляется путем проведения соответствующих измерений или контроля, поэтому методике контроля отводится исключительная роль.
Основные требования, предъявляемые к контролю, заключаются в следующем.
1. Вероятность того, что доброкачественное изделие будет забраковано, должна иметь некоторое определенное значение, которое будет определяться чувствительностью и точностью применяемых методов и аппаратуры.
2. Вероятность принятия изделия низкого качества (дефектного) должна иметь некоторое определенное значение, зависящее от квалификации контролеров, эффективности применяемых методов и аппаратуры.
3. Применяемый метод или аппаратура должны обеспечить непрерывность проведения контроля технологических процессов.
4. Метод и аппаратура должны обеспечить сплошной контроль всех выпускаемых изделий.
Контроль по своим признакам может быть разрушающий, неразрушающий (неповреждающий), аналитический, метрологический (поверочный). В настоящее время наиболее широкое распространение получили разрушающие и аналитические методы. Основное их достоинство заключается в том, что они дают возможность определить объективные абсолютные параметры материалов и изделий. Такой важный параметр изделия, как прочность, наиболее объективно определяется путем его разрушения с соблюдением режимов нагружения, вида нагрузки и обеспечения условий окружающей среды (температура, влажность).
Аналитические методы в большинстве случаев являются также разрушающими, так как связаны с взятием проб или изготовлением специальных образцов. Они отличаются высокой точностью измерения. Основные недостатки разрушающих и аналитических методов контроля заключаются в следующем:
– не выполняют всех требований, предъявляемых к контролю (требование 4), так как для их выполнения пришлось бы разрушить все изделия;
– не позволяют выявить изменение свойств конкретного изделия при воздействии на него внешних факторов (температуры, нагрузок, влаги и т. д.) в процессе эксплуатации;
– не обеспечивают непрерывности измерений при контроле кинетики или динамики технологических процессов изготовления изделий;
– не дают возможности определить реальную изменчивость свойств материала непосредственно в изделии на различных его участках без вырезки образцов;
– не позволяют выявить внутренние дефекты в материале изделия без его разрезки.
Метрологический контроль служит в основном для контроля (поверки) методов контроля и направлен на определение точности и чувствительности применяемых методов и аппаратуры.
Неразрушающие физические методы контроля (НФМК) в последнее время все более активно начинают применяться в производстве изделий из КМ. Они вполне удовлетворяют всем требованиям, предъявляемым к контролю, и не имеют недостатков, присущих разрушающим и аналитическим методам. В соответствии с ГОСТ 18353-73, принято 10 видов неразрушающего контроля: акустический, капиллярный, магнитный, оптический, радиационный, радиоволновой, тепловой, течеисканием, электрический, электромагнитный (вихревых токов) [18]. Каждый из указанных видов подразделяется на большое количество методов.
Однако неразрушающие методы контроля являются косвенными, т. е. не позволяют проводить прямой численный отсчет таких параметров, как прочность и структура. Для определения этих параметров неразрушающими методами необходима их трактовка при помощи разрушающих или аналитических методов. Даже при дефектоскопии для проверки правильности контроля производят вскрытие (трепанацию) отдельных изделий. Тарировка методов дефектоскопии проводится по специальным эталонам с заранее заложенными дефектами.
Точность и чувствительность неразрушающих методов контроля зависят от точности и чувствительности методов, при помощи которых проводится их тарировка, и оптимальности выбранного сравнительного эталона. Отсюда важнейшими задачами неразрушающего контроля являются анализ физических основ взаимодействия используемых излучений (ультразвука, радиоволн, радиации, магнитных и электрических полей и др.) с контролируемой средой и разработка методики контроля конкретных параметров технологических процессов и готовых изделий при их изготовлении и эксплуатации.
К НК предъявляются следующие основные общие требования:
– возможность осуществления эффективного контроля на различных стадиях изготовления, в эксплуатации и при ремонте изделий;
– возможность контроля качества продукции по большинству заданных параметров;
– согласованность времени, затрачиваемого на контроль, со временем работы другого технологического оборудования;
– высокая достоверность результатов контроля;
– возможность механизации и автоматизации контроля технологических процессов, а также управления ими с использованием сигналов, выдаваемых средствами НК;
– высокая надежность дефектоскопической аппаратуры и возможность использования ее в различных условиях;
– простота методики контроля, техническая доступность средств контроля в условиях производства, ремонта и эксплуатации.
1.2 Анализ эффективности методов контроля качества
Выбор того или иного метода контроля качества определяется следующими факторами [27]:
– агрегатным состоянием контролируемой среды (газообразное, жидкое, твердое);
– физическим состоянием контролируемой среды (диэлектрик, полупроводник, магнетик, парамагнетик и пр.);
– видом структуры контролируемой среды (аморфная, монокристаллическая, поликристаллическая, крупноструктурная неоднородная, изотропная или анизотропная и т. д.);
– способностью взаимодействовать с проходящим излучением (слабое или сильное поглощение, слабое или сильное рассеяние и т. д.);
– методологией контроля (в вакууме, в жидкости, при высокой температуре, под большим давлением и т. д.);
– размером, конфигурацией и конструктивными особенностями объекта контроля (мало-, средне-, крупногабаритный, простой или сложной формы, одно- или многослойная и т. д.);
– видом решаемой задачи (дефектоскопия, толщинометрия, диагностика прочности, контроль кинетики отвержения, контроль напряженно-деформированного состояния, контроль содержания компонентов и др.).
Композиционные материалы – весьма сложный объект контроля, так как характеризуются существенной неоднородностью структуры, анизотропией свойств, большим разнообразием типов армирования (однонаправленный, продольно-поперечный, комбинированный и др.), специфическими физическими свойствами: высокими электроизоляционными качествами, низкой теплопроводностью, звукоизоляцией, большим разбросом физико-механических характеристик, малыми значениями плотности (0,02-2,0 г/см3). Большинство видов композиционных материалов в зависимости от используемого вида наполнителя относятся к диэлектрикам или плохим проводникам. Практически все композиты являются немагнитными материалами, поэтому методы контроля, используемые при дефектоскопии изделий из металла, например магнитные и токовихревые, в большинстве случаев не подходят для дефектоскопии изделий из композиционных материалов. Однако эти методы могут быть применены для толщинометрии таких изделий. Не эффективны для контроля композитов также высокочастотные ультразвуковые методы, так как ультразвуковые волны с частотой выше 1 МГц либо невозможно ввести в контролируемую среду из-за их сильного поглощения и рассеяния и существенной шероховатости поверхности, либо они значительно ограничивают диапазон контролируемых значений толщины.
Радиационные методы более эффективны для контроля плотности или толщины композитов, чем для дефектоскопии, так как чувствительность их дефектоскопии данными методами при равнозначной энергии излучения в 3–4 раза ниже чувствительности дефектоскопии стали. Следует также отметить, что для этого метода контроля композиты могут находиться как в твердом, так и в пастообразном (полуфабрикат), жидком или гелеобразном (связующее) состояниях [22].
В результате анализа и оценки эффективности существующих методов нарушающего контроля установлено, что наиболее эффективными при неразрушающем контроле композитов являются следующие:
– низкочастотный ультразвуковой импульсный;
– радиационный;
– инфракрасный оптический;
– теплометрический;
– электрический.
Основные критерии, обусловливающие выбор данных методов контроля:
– безопасность для обслуживающего персонала, чувствительность контроля;
– точность и воспроизводимость результатов контроля;
– возможность механизации и автоматизации контроля;
– обеспечение высокой производительности контроля;
– сравнительная простота методики контроля;
– информационная способность и универсальность контроля;
– наличие и возможность использования серийной аппаратуры;
– сравнительно невысокая стоимость контроля;
– возможность использования обслуживающего персонала невысокой квалификации.
Указанные методы контроля можно использовать как индивидуально, так и в комплексе. Следует учитывать, что увеличение количества используемых методов наряду с повышением чувствительности и информативности контроля приводит также к повышению стоимости и снижению производительности контроля. Наиболее эффективным комплексом может быть совокупность низкочастотного ультразвукового и радиоволнового методов или низкочастотного ультразвукового и электрического методов. С повышением требований к контролю число методов в комплексе может возрастать.
В этом случае оптимальным будет сочетание низкочастотного ультразвукового, радиоволнового и теплометрического методов [4].
Выбранные методы позволяют определять непосредственно в изделии большое количество различных физических характеристик:
– скорость и затухание упругих волн (продольных, сдвиговых, изгибных, поверхностных);
– коэффициенты прохождения, отражения и преломления данных упругих волн;
– угол поворота плоскости поляризации сдвиговых волн;
– электропроводность;
– диэлектрическую проницаемость и тангенс угла электрических потерь; коэффициенты затухания, прохождения, отражения и преломления электромагнитных волн инфракрасного (ИК) диапазона;
– коэффициенты тепло- и температуропроводности и др.
Данные характеристики, определяемые непосредственно в изделии, могут быть использованы для прямой и косвенной оценки таких параметров, как прочность и жесткость изделий, прочность и упругие свойства материала, плотность, структура, состав компонент, вязкость, степень отверждения, геометрические размеры, влажность, напряженно-деформированное состояние и др.
Таким образом, при комплексном контроле решается ряд задач.
1. Определяется оптимальный комплекс физических параметров, по которому оцениваются прочность и другие физико-механические характеристики композита и изделий на их основе.
2. Разрабатывается и осуществляется оптимальный комплекс методов и средств контроля дефектов структуры.
3. Дается интегральная оценка работоспособности изделия по комплексу параметров, определенных неразрушающими методами.
Определение указанных характеристик в процессе переработки композитов в изделия позволяет устранить причины, вызывающие нарушения структуры, образование дефектов и изменчивость свойств материала в изделии.