Полимерные седла поворотной арматуры. Современные подходы к выбору и изготовлению
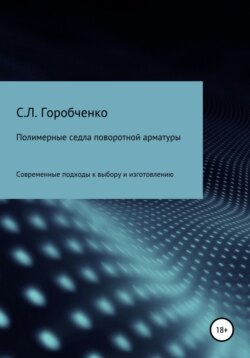
000
ОтложитьЧитал
Введение
В свое время широкое распространение шаровые краны получили именно благодаря созданию полимерных седел, способных удерживать высокие давления и температуры и обеспечивать требуемую герметичность. Это произошло в 30-е годы 20-го века, когда был изобретен тефлон. С его широким распространением начали производиться в большом количестве и шаровые краны с мягкими уплотнениями.
Сегодня шаровые краны и дисковые затворы с полимерными уплотнениями нашли свою нишу и успешно конкурируют с поворотной арматурой с эластомерными уплотнениями и уплотнениями металл по металлу. Многие компании научились производить уплотнения как самостоятельно, так и используют уплотнения, производимые специализированными компаниями. Количество марок полимеров, особенно на основе фторопластов, каждый год прибавляется. Они обеспечивают работу арматуры в разных условиях эксплуатации, и для этого в них формируют специфический подбор механических и антикоррозионных свойств и других свойств в зависимости от требований заказчика.
Современный подход к выбору и изготовлению уплотнений и седел шаровых кранов и дисковых затворов, а также другой поворотной арматуры предполагает хорошее знание материалов, типов затворов арматуры, технологий изготовления и проблем, которые могут возникнуть в связи с неправильным выбором оптимального типа материала седла, отсутствием соответствующих нагрузок расчетов, отклонений качества уплотнения в связи с несовершенством технологии.
Большую роль в развитии использования полимерных седел начинают играть 3D-технологии моделирования и изготовления уплотнений методами 3D-печати. Особенно важно представить именно эту технологию, поскольку традиционные виды технологии, такие как изготовление методами механической обработки из трубной заготовки, спекание на горячих прессах, литье на термопластавтоматах имеют значительные ограничения как капиталоемкости такого производства, рассчитанного в целом на высокую серийность и массовость потребления, по срокам изготовления, трудоемкости технологической подготовке производства и использованию ограниченного ассортимента уплотнений достаточно простых форм.
Роль новых видов изготовления уплотнений возрастает с ростом используемых номинальных диаметров поворотной арматуры. Уже сейчас средние диаметры на многих непрерывных крупнотоннажных производствах превышают DN300-500мм. Размеры в 1500 мм уже не являются редкостью, а некоторые виды шаровых кранов уже работают на диаметре 1640мм. Для дисковых затворов такие размеры только самое начало. На крупных металлургических производствах можно встретит поворотные дисковые затворы диаметров и 2000 и даже 4000 мм. Здесь традиционная технология изготовления полимерных уплотнений и седел начинает сдавать свои позиции.

Рис.1.1. Уплотнения шарового крана DN 800мм, Констафтор 300С [1]
Проблема применения пластмасс охватывает ряд вопросов от выбора материала, типа конструкции, выбора способа изготовления, оборудования, разработки технологии изготовления, испытания, расчета экономической эффективности. Подход к выбору применения пластмасс в уплотнениях и седлах арматуры должен быть системным, охватывающим все этапы от выбора пластмасс до изготовления уплотнений.
Выбор пластмасс основывается на знании эксплуатационных, определяющих работоспособность пластмасс в условиях эксплуатации в арматуре, и технологических свойств, определяющих поведение пластмасс при переработке различными методами. Для рационального выбора важна систематизация условий эксплуатации требований к эксплуатационным свойствам пластмасс в уплотнениях. Процедуру выбора пластмасс облегчает анализ основных свойств различных, уже применяющихся пластмасс, их преимуществ и ограничений по применению, а также классификация пластмасс по эксплуатационному назначению с рекомендациями по их рациональному применению. При подборе должны учитываться методы переработки, условия подготовки к переработке и формованию.
Рациональный подбор основывается на знании марочного ассортимента полимеров и анализе тенденций изменения их свойств при создании композиционных материалов. В курсе приводятся основные данные, необходимые для выбора материала для уплотнений. Большое внимание мы уделим перспективным технологиям и разработке новых видов конструктивных решений на основе понимания законов развития технических систем.
Задачей, поставленной в представленном материале является:
– предоставить обзор современных конструкций затворов и используемых материалов;
– показать направления развития технологий применения и изготовления полимерных уплотнений поворотной арматуры;
– представить новые решения на основе моделирования на основе методов МКЭ в программной оболочке ANSYS;
– дать представление о возможностях 3D-печати в области создания новых типов уплотнений.
Раздел 1. Обзор применяемых затворов
1.1. Затворы шаровых кранов и клапанов
Шаровые краны могут иметь плавающий шар и шар в опорах (с фиксированной осью). Уплотнение затвора в кранах с плавающим шаром происходит путем самоуплотнения, так как шар под действием давления рабочей среды прижимается к седлу. Такие конструкции для управления требуют больших крутящих моментов, а, следовательно, приводов большой мощности.
В кранах больших размеров, например, в магистральных шаровых кранах, предпочтительны конструкции с шаром в опорах. При этом шар с двумя цапфами поворачивается вокруг фиксированной оси, образованной двумя цапфами, а уплотнение осуществляется подвижными седлами, поджимаемыми к шару пружинами, расположенными по окружности седла, или резиновым поджимным кольцом, Уплотнительные кольца, установленные на седле, могут изготовляться из резины, фторопласта, капролона, фторопласта с наполнителями, полиуретана, терморасширенного графита или бронзы. Высокие эксплуатационные качества показали
уплотнительные кольца из резины, марка которой подбирается в зависимости от условий эксплуатации крана.
Непременным условием работоспособности резиновых колец является высокая твердость резины. Хорошо зарекомендовали себя резиновые уплотнительные кольца, покрытые фторопластовой пленкой.
Для уплотнительных колец и уплотнений по штоку используется чистый или наполненный фторопласт, как химически стойкий, так и обладающий низким коэффициентом трения (менее 0,1). Однако фторопласт теряет свои свойства при температурах выше 100°С, а при температуре 230°С его стойкость падает до 00С. Это вынудило использовать графики зависимости рабочего давления от температуры для мягких уплотнений кранов. Указанная зависимость для чистого фторопласта регламентирована BS 5351 (рис. 1.2.).
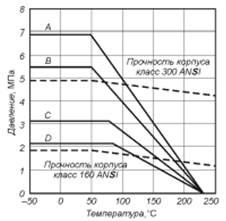
Рис. 1.2. Зависимость рабочего давления в шаровых кранах с уплотнениями
из чистого фторопласта от температуры: А – 2”; B – 3“; C – 6”… 8”; D – 10”… 8”
Нейлоны, полиэстер кетоны (РЕЕК), флубон и другие модификации фторопласта, графитовые уплотнения, обычно терморасширенный графит, используются для повышения стойкости при высоких давлениях и температурах.
В табл. 1.1 приведены конструкции подвижных седел шаровых кранов с пробкой в опорах.
Таблица 1.1. Конструкции подвижных седел шаровых кранов с шаром на опорах
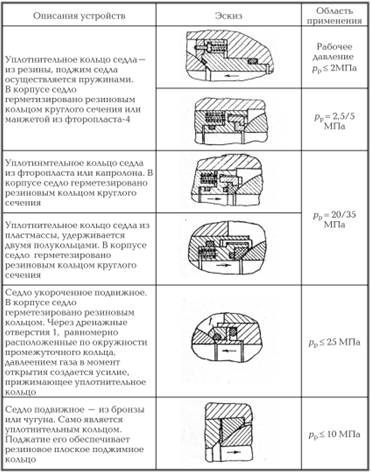
В связи с повышенными усилиями, действующими на седлах шаровых кранов больших диаметров прохода, и значительным износом уплотнительных поверхностей под действием этих усилий в некоторых конструкциях предусматривается автоматический отжим уплотнительных колец давлением рабочей среды (газом в газовых магистральных кранах) перед поворотом шара и подача густой смазки в затвор. Эти действия выполняются автоматически, что предусмотрено системой управления краном, имеющей сложную схему и включающей соответствующие блоки управления, электромагнитные клапаны и другие элементы.
Подвижные седла, снабженные уплотнительными кольцами, расположены в цилиндрических расточках корпуса крана.
Для больших перепадов давления, особенно в шаровых кранах, работающих в режиме дросселирования, применяются многослойные уплотнения, состоящие из чередующихся колец, изготовленных из металла и терморасширенного графита (рис. 1.3).

Рис. 1.3. Многослойное уплотнение шарового крана
Получая возможность расширяться, проходя через входное сечение, или сжиматься на выходе, поток испытывает пульсации давления, следуя мимо слоев металла и графита. Процесс аналогичен происходящему в многоступенчатом редукционном клапане, в данном случае каждый слой графита воспринимает только частичную нагрузку от общего перепада давления.
Многослойная конструкция уплотнительных колец металл – графит позволяет эксплуатировать шаровые краны при температурах 400…600 °С.
1.2. Уплотнения дисковых затворов
Наиболее распространенными конструкциями этой арматуры являются дисковые затворы с дисками, расположенными соосно с осями трубопроводов и приводных валов. В этих затворах устанавливаются вкладыши из синтетического каучука, которые защищают материал корпусов от коррозии и выполняют функции обеспечения герметичности в основных седлах и уплотнениях валов. Марка синтетического каучука для вкладышей выбирается в зависимости от рабочей среды и ее параметров. В качестве примера на рис. 1.4 показана конструкция дискового затвора Санкт-петербургской фирмы «Арматэк».
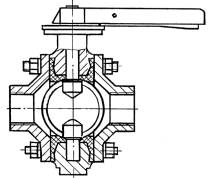
а)
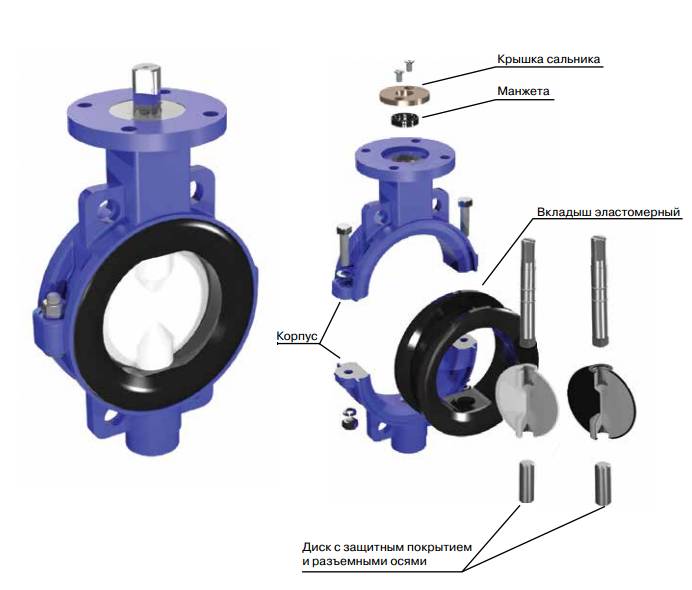
б)
Рис. 1.4. Дисковый затвор с эластичным вкладышем
а) – общий чертеж
б) – общий вид и отдельные элементы конструкции
В дисковых затворах с эксцентрично расположенными дисками без эластичных вкладышей валы или цапфы размещаются в области, определяемой перпендикулярами к образующей уплотнительного конуса, восстановленными из точки, расположенной у входа в уплотнительный конус длинной стороны диска (наружной образующей конуса уплотнения большего диаметра), и на меньшем диаметре конуса, аналогично показанной для обратных затворов.
Уплотнения могут выполняться без эластомерных элементов (металл по металлу), с кольцами, установленными в седлах (рис. 1.5) или на дисках (рис. 1.6). Применяются кольца как круглого, так и некруглого сечения.
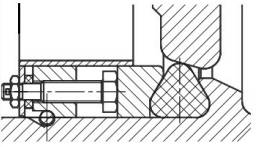
Рис. 1.5. Эластомерное кольцо, установленное в седле
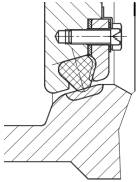
Рис. 1.6. Эластомерное кольцо, установленное на диске
Перспективными показали себя многослойные уплотнения, устанавливаемые в корпусе (рис. 1.7) или в диске (рис. 1.8). В уплотнительных пакетах поочередно устанавливаются кольца из металла и мягкого уплотнительного материала, для использования на высокотемпературных средах и для пожаробезопасной арматуры применяется терморасширенный графит.
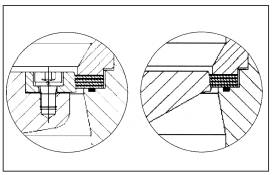
Рис. 1.7. Уплотнение, установленное в корпусе (фирма Samson):
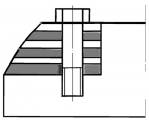
Рис. 1.8. Уплотнение, установленное в диске
Запирающие элементы
Запирающие элементы служат для герметичного перекрытия отверстий в седлах корпусов запорной арматуры. К запирающим элементам относятся золотники и тарелки в клапанах, диски и клинья в задвижках, пробки, в т.ч. шары, в кранах, диски в запорных и обратных поворотных затворах. Форма и размеры запирающих элементов определяются конструкцией и размерами арматуры.
Простую форму имеют запирающие элементы клапанов, они представляют собой диски с элементами присоединения к штоку. В некоторых конструкциях клапанов малого диаметра роль запирающего элемента выполняет нижняя конусная часть шпинделя или штока. Наиболее сложную конструкцию имеют клинья задвижек большого диаметра.
На запирающем элементе должны быть предусмотрены четыре следующие основные устройства: пластина для перекрытия прохода в седле, уплотнительные поверхности для герметизации, присоединение к шпинделю или штоку и направляющие устройства для направления в корпусе или по крышке. В некоторых конструкциях арматуры последнее может отсутствовать, например, в клапанах малых размеров, кранах, заслонках, мембранных клапанах и шланговых задвижках.
Направление золотника (тарелки) может быть нижним – «перья» золотника направляются в отверстии седла, или верхним – тело золотника направляется в расточке корпуса или крышки. В запирающих элементах задвижек предусматриваются пазы или гребни, которые направляются соответствующими выступами или пазами в корпусе. Пробка конусного или цилиндрического крана направляется в корпусе своей рабочей поверхностью. В шаровом кране шар может быть плавающим – при малых DN, или в опорах – при больших. В последнем случае шар направляется своими цапфами, расположенными в подшипниках корпуса и крышки. В затворах диски закреплены на валу, и этим определяется их расположение в корпусе.
Уплотнительные поверхности на запирающих элементах могут выполняться без вставных колец – из материала детали, – со вставными кольцами и с наплавленной кольцевой поверхностью.
Вставные уплотнительные кольца могут изготавливаться из латуни, бронзы, никелевых сплавов, коррозионностойкой стали, резины, фторопласта, полимеров или кожи. Материал уплотнительных колец выбирается в зависимости от физических и химических (коррозионных) свойств рабочей среды и ее энергетических параметров (давление, температура).
На запирающий элемент действуют перестановочное усилие, создаваемое шпинделем или штоком (с учетом силы герметизации), и давление рабочей среды, что должно быть учтено при расчете на прочность. В связи с большими усилиями в задвижках с большими диаметрами прохода и дисковых затворах предусматривают ребра жесткости и упрочняющий обод по окружности диска.
Ресурс арматуры часто определяется ресурсом запирающего элемента, поскольку он в большинстве случаев работает в наиболее сложных условиях: целиком погружен в рабочую среду, подвергается коррозии, его уплотнительные поверхности изнашиваются. В особо сложных условиях работают запирающие элементы энергетической дроссельной арматуры, которые подвергаются интенсивному эрозионному и кавитационному изнашиванию, что приводит к ускоренному выходу из строя. Для повышения срока службы рабочие поверхности на них наплавляются сплавами повышенной стойкости.
Применяются различные конструкторские решения – многокаскадное дросселирование, дробление струи для гашения энергии (перфорированные или клеточные рабочие органы).
Раздел 2. Материалы для изготовления уплотнений
2.1. Кратко о полимерах
Полимеры – это вещества, макромолекулы которых состоят из многочисленных элементарных звеньев – мономеров одинаковой структуры. Их молекулярная масса может составлять от 5000 до 1000000 ед. Полимеры состоят из цепочек из отдельных звеньев, что задает гибкость, но она ограничена размерами элементов и жесткостью звеньев.
Сцепление полимеров обеспечивается степенью жесткости связей. Так, основные атомные цепи обладают жесткой ковалентной связью, с энергией связи до 330 кДж/моль. Межмолекулярные цепи по своей физической природе обладают водородной связью на основе притяжения молекул водорода и когезии. Энергия связи составляет от 5 до 40 КДж/моль.
Полимеры построены из одинаковых по структуре звеньев. Сополимеры состоят из разнородных звеньев. Одним из свойств полимерной структуры является стереорегулярность – это свойство правильного расположения звеньев в пространстве. Это свойство определяет повышенные свойства полимеров.
КЛАССИФИКАЦИЯ ПОЛИМЕРОВ
Полимеры делятся:
1. по составу
2. по форме макромолекул
3. по фазовому состоянию
4. по полярности
5. по отношению к нагреву.
По составу полимеры делятся на органические, элементоорганические и неорганические.
Органические полимеры наиболее используемы, их основная цепь образована углеродными атомами (карбоцепные полимеры). В гетерогенных полимерах связь образована кислородом, фосфором и хлором. Кислород придает связи гибкость, фосфор и хлор – огнестойкость, сера – газонепроницаемость, фтор – химическую стойкость
Элементоорганические полимеры – это полимеры, основная цепь которых образована атомами кремния, титана, алюминия с группами СН3, СН6, СН2. Металлы придают полимеру теплостойкость как карбонильные группы – эластичность. В основном используются кремнийорганические полимеры.
Неорганические полимеры – это силикатные стекла, керамика, слюда, асбест и др. Их основу составляют оксиды кремния, алюминия, магния, кальция и др. Внутриатомная связь – ковалентная, цепи между собой образуют ионную связь. Этот вид полимеров обладает высокой плотностью, длительной теплостойкостью, но и высокой хрупкостью. Характерный представитель – силикаты.
Смешанные полимеры – это класс композитов. Характерный представитель – стеклопластик.
По форме линейные полимеры делятся на линейные, разветвленные, плоские, ленточные (лестничные) и пространственные (сетчатые). Виды полимеров по форме приведены ниже, рис.2.1.
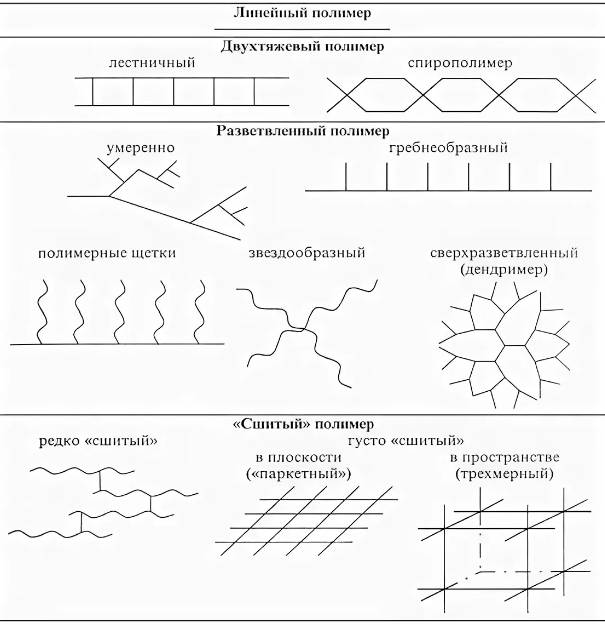
Рис. 2.1. Формы линейных полимеров
Линейные полимеры образуют прочную связь вдоль цепи и имеют слабую межмолекулярную связь. Это придает им высокую эластичность, способность размягчаться и затвердевать. Характерный представитель – полиамиды. Виды
Лестничные полимеры имеют более жесткую цепь, что придает им свойство повышенной теплостойкости, жесткости и малой растворимости.
Пространственные полимеры образуются при сшивке макромолекул. Они не плавятся и не растворяются, обладают высокой упругостью. Делятся на редкосетчатые – имеющие высокую упругость (мягкие резины), густосетчатые, имеющие высокую твердость и теплостойкость. К ним относятся большинство конструкционных пластиков. К паркетным полимерам относится графит.
По фазовому состоянию полимеры делятся на аморфные и кристаллические. Для кристаллических полимеров характерно появление надмолекулярных структур.
Аморфные полимеры однофазны, собраны из цепных молекул в пачки, которые состоят из многих рядов макромолекул. Они способны перемещаться.
Глобулы – это свернутые в клубки цепи, они имеют невысокие свойства, для них характерна хрупкость по границам зерен из-за недостаточной связи.
Кристаллические полимеры образуются из гибких регулярных структур при фазовом переходе внутри пачки и формируют пространственные решетки кристаллов.
Образование кристаллической структуры происходит следующим образом:
1. складывание гибких пачек в ленты
2. соединение лент друг с другом с образованием пластин
3. наслоение пластин друга на друга с образованием правильных структур.

Рис. 2.2. Образование полимера полистирола из мономера
Сферолиты образуются при затрудненном образовании объемных кристаллов из меньших структур. Происходит чередование кристалличных и аморфных участков в виде лучей.
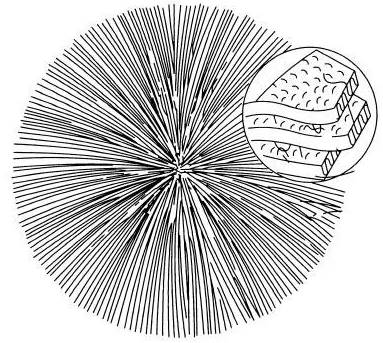
Рис. 2.3. Сферолиты с образованием из пластин. Масштаб – несколько мкм.
Свойствами кристаллических структур являются организованность, термодинамическая стабильность, большое время жизни без нагрузки.
Обычно в полимерах встречается двухфазная структура. Кристалличность придает ей жесткость, твердость и теплостойкость. Однако, надмолекулярные структуры при длительном хранении, эксплуатации или переработке подвержены изменениям и распаду.
По полярности полимеры делятся по наличию диполей центров распределения положительного или отрицательного зарядов. Условиями образования полярности являются:
1. наличие полярных связей (-Cl, – F, +OH)
2. несимметрия в структуре по силе связей: C-H < C-N < C-O < C-F< C-Cl.
Неполярные полимеры, как правило, углеводороды, являются диэлектриками и обладают морозостойкостью. Полярные полимеры обладают жесткостью, теплостойкость, но низкой морозостойкостью.
По отношению к нагреву полимеры делятся на термопластичные и термореактивные.
Термопластичные полимеры размягчаются при нагреве, плавятся и затвердевают обратимо. Они имеют линейную или разветвленную структуру.
Термореактивные полимеры сначала линейны и размягчаются. Затвердевают из-за химических реакций с образованием пространственной структуры и остаются твердыми в термостабильном состоянии.
ОСОБЕННОСТИ СВОЙСТВ ПОЛИМЕРНЫХ МАТЕРИАЛОВ
Особенности полимерных материалов
1. неспособность переходить в газовую фазу из-за высокой молекулярной массы
2. полидисперсность – она определяет значительный разброс механических свойств
3. зависимость от структуры и эксплуатационных условий.
Полимеры могут находиться в нескольких основных состояниях:
Стеклообразное – это твердое, аморфное состояние, где колебания атомов происходят без колебания цепей.
Высокоэластичное – обратимое изменение формы при небольших нагрузках, происходит из-за изгиба макромолекул
Вязкотекучее – жидкое состояние с высокой вязкостью, при котором подвижна вся макромолекула. Состояние вязкотекучести определяется по термомеханическим кривым.
Для пространственных полимеров характерно стеклообразное состояние. Для редкосетчатых полимеров характерно стеклообразное и высокоэластичное в вязкотекучем состоянии. Характерным является область упругих деформаций и после превышения предела вынужденной эластичности. При небольших напряжениях происходит перемещение отдельных сегментов макромолекул и их ориентация в направлении действующей силы. Так, в резинах узлы сетки препятствуют перемещению полимерных цепей. Происходит переход в высокоэластичное состояние до химического разложения без вязкотекучести.
Кристаллические полимеры тверды до температуры кристаллизации, но имеют разную жесткость из-за наличия аморфных участков.
Полимеры с плотной сетчатой структурой имеют характеристики кривой деформация – растяжение, соответствующее упругим деформациям с небольшими значениями. Высокоэластичная деформация практически отсутствует. Кристаллические полимеры имеют зоны упругой деформации с образованием шейки разрыва на образце, участок значительной деформации за счет распространения шейки на всю длину образца и участок разрыва.
Для полимеров характерно т.н. ориентационное упрочнение, когда при медленном растяжении в высокоэластичном или вязкотекучем состоянии макромолекулы и надмолекулярная структура ориентируется в силовом поле. При этом усиливается межмолекулярное взаимодействие, повышается температура стеклования, уменьшается температура перехода к хрупкости и повышается прочность. Появляется анизотропность вплоть до расслоения. Прочность может увеличиваться в 2-5 раз в продольном направлении и снижаться на 30-50% в поперечном. Модуль упругости возрастает в 2 раза. Кристаллические участки в полимере улучшают свою структуру с повышением прочности, тогда как аморфные участки дезориентируются.
Релаксационные свойства полимеров – это свойства, зависящие от времени, действия и скорости приложения нагрузки из-за раскручивания и распрямления цепей и перемещения макромолекул. Скорость релаксации составляет до 10 -4 и может продолжаться сутками и месяцами. Релаксационную способность полимеров определяют по релаксации напряжений при неизменном удлинении.
В линейных полимерах релаксация связана с перемещением макромолекул относительно друг друга до снижения внешнего напряжения до нуля. В сетчатых полимерах релаксация чаще всего не происходит до определенного момента, когда нет нарушений связей, и полимер продолжает удерживать приложенное напряжение.
Полимеры склонны к ползучести, когда при снятии нагрузки остается пластическая деформация. У сетчатых полимеров происходит релаксация напряжений до нуля без образования деформационных участков.
Долговечность полимера определяется силой энергии связи в цепи, состоянием структуры, приложенным напряжением и температурой. При повышении приложенного напряжения и температуре долговечность падает и эта зависимость сильнее, чем у металлов.
Старение полимеров – это самопроизвольное необратимое уменьшение технических характеристик со временем. Причиной являются воздействие света, теплоты, кислорода, озона, многократные деформации и влага. Для определения способности противостоять старению проводят испытания: естественное в атмосфере, тепловое при Т<Тпл на 500С до 50% снижения характеристик.
Причиной старения является образование сложных радикалов с деструкцией полимера из-за окисления кислородом или структурирование. Деструкция приводит к размягчению, выделению летучих веществ (каучук). Структурирование, напротив, приводит к увеличению твердости, хрупкости, потери эластичности (полистирол). Тепловое старение наблюдается при температурах 200-5000С и выше с образованием газовой фазы из-за разложения компонентов во всем объеме.
Термостабильны полиэтилен, полифенолы. Они обладают высокой теплотой полимеризации или высокой степенью полярности, как фторполимеры. Устранение склонности к старению достигается добавкой органических стабилизаторов и антиоксидантов (амины, фенолы). Это приводит к значительному увеличению срока службы. Так, для полиэтилена, стабилизированного сажей, можно увеличить срок службы более 5 лет, поливинилхлорида до 10-25 лет.
Радиационная стойкость – способность противостоять ионизации и возбуждению, из-за которых происходит разрыв связей и образование свободных радикалов. Основными вредными проявлениями являются сшивание цепей или деструкция. При сшивании увеличивается молекулярная масса, повышается теплостойкость и механические свойства.
При деструкции происходит снижение молекулярной массы и уменьшение прочности. Деструкция характерна для полипропилена, полиэтилена и полиамида. Наиболее устойчивы к радиации бензолы (полистирол). Устранение вредного влияния радиации достигается введением антирадов – ароматических аминов, устраняющих энергию возбуждения и обеспечивающих ее рассеяние.
Вакуумстойкость полимеров. При вакуумировании возможно ухудшение свойств из-за выделения добавок из материала (пластификаторов, стабилизаторов) и деструкция. К примеру, это может быть деполимеризация. К потере вакуумстойкости склонны полиэтилен, полипропилен, полиамиды. Оценка вакуумстойкости проводится по газопроницаемости, газовыделению и вакуумплотности.
Газопроницаемость – это способность пропускать газ через уплотнитель. На газопроницаемость влияют состав, структура, природа газа, температура. Газопроницаемость меньше у полярных и линейных полимеров, выше у гибких макромолекул, при введении пластификаторов, и в меньшей степени при введении минеральных наполнителей.
Абляция – разрушение материала, сопровождаемое уносом его массы газовым потоком.
Ее характеризуют через абляционную стойкость. Она определяется устойчивостью к механической, тепловой и термоокислительной деструкции. Для линейных полимеров характерна низкая стойкость к деструкции и деполимеризации, для лестничных и сетчатых характерно структурирование и обезуглероживание. Для повышения абляционной стойкости материала, его армируют более теплопроводящими материалами, например, железом.
Адгезия – это слипание разнородных тел из-за межмолекулярного взаимодействия. Это явление используется при нанесении пленок и покрытий. Для полимеров может встречаться и аутогезия – самослипаемость. Ее причинами являются адсорбция, электростатическое притяжение, диффузия макромолекул.
ПЛАСТИЧЕСКИЕ МАССЫ
Пластмассы – массы, получаемые на основе органических полимерных связующих. Они способны при нагреве быть пластическими, а отверждаются при дальнейшем нагреве или охлаждении.
Состав, классификация и свойства пластмасс.
В состав пластических масс входят:
1. Связующие (синтетические смолы, эфиры, целлюлозы) и наполнители – порошкообразные или волокнисты. При пропитке наполнителя связующими и их опрессовывании получается монолитная масса.
2. Наполнители служат для повышения механических свойств, снижения усадки и придания специфических свойств.
3. Пластификаторы повышают эластичность и облегчают обработку.
4. Отвердители – амины
5. Катализаторы – перекисные соединения для ускорения отвержения термореактивных полимеров
6. Ингибиторы предохраняют массы от самопроизвольного отвержения
7. Красители.
Свойства пластмасс определяются составом компонентов, сочетанием компонентов и их количественным соотношением.
Классификация пластмасс.
Пластмассы классифицируют
1. по типу связующего
1.1. термопласты – удобны, усадка менее 1-3%, упруги, нехрупки, способны ориентироваться и иметь ориентационное упрочнение.
1.2. реактопласты – хрупки, усадка до 10-15%, для повышения их свойств вводят усиливающие или пластифицирующие наполнители.
2. По виду наполнителя
2.1. порошковые (карболиты) – наполнителем является древесная мука, графит, тальк
2.2. волокнистые – в качестве волокна используют очесы хлопка или льна, стекловолокно, асбест.
2.3. слоистые – используют листовые наполнители
2.4. газонаполненные – пено-поропласты, где наполнителем является воздух или нейтральные газы.
3. По применению
3.1. силовые – конструкционные, фрикционные и антифрикционные, электроизоляционные
3.2. несиловые – прозрачные, химически стойкие, электроизоляционные, декоративные, уплотнительные.
Особенности пластмасс
Их достоинствами являются:
1. малая плотность 1-2 т/м3
2. низкая теплопроводность 0.1 – 0,3Вт/мК
3. Электроизоляционные свойства
4. химическая стойкость
5. антифрикционность
6. прочность
7. технологичность.
Недостатками являются:
1. низкая теплостойкость
2. высокое тепловое расширение (в 10-30 раз больше, чем у стали)
3. низкая упругость и вязкость
4. склонность к старению
ТЕРМОПЛАСТИЧЕСКИЕ МАССЫ
Термопласты – полимеры линейной или разветвленной структуры, иногда с пластификатором. Свойства – Траб – обычно не выше 60-700С, теплостойкие до 150-2500С, термостойкость с жесткими цепям и циклическими структурами – до 400 – 6000С.
Особенности эксплуатации – при эксплуатации происходит снижение прочности и вынужденная эластичность при длительном статическом нагружении. – повышение хрупкости с ростом скорости деформации. Прочность – 10-100МПа, модуль упругости 1,8-3,5х103 МПа. Хорошо сопротивляются усталости сигма 0,2-0,3 от предела прочности.
Виды термопластов – полярные и неполярные. Неполярные – полиэтилен, полипропилен, полистирол, фторопласт 4. Полярные термопласты – фторопласт 3, ПВХ, полиамиды, полиуретаны, полиэтилентерефталаты, поликарбонаты, полиакрилат, пентапласты, полиформальдегиды.
Термостойкие пластики
Термостойкость обеспечивается за счет введения фениленовых звеньев, что обеспечивает работоспособность при 4000С и при замене гибких звеньев на жесткие гетероциклические, что повышает Траб до 6000С. Виды термостойких пластиков: ароматические полиамиды, полифениленоксид, полисульфоны, гетероциклические полиимиды.
Термопласты с наполнителями
Связующим является полимерная основа. Наполнители – стекловолокно, асбест, органические волокно, углеродные волокна и пр. Волокнистые наполнители образуют каркас и упрочняют материал. Промышленное использование имеют полиамиды и поликарбонаты, наполненные рубленным стекловолокном. Это повышает прочность до 90-149 МПа, обеспечивает повышенное сопротивление усталости и износу при Тисп 60-1800С.