Аналитический обзор по снижению негативного воздействия пылевидных отходов на окружающую среду
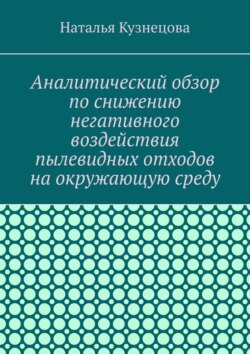
000
ОтложитьЧитал
© Наталья Кузнецова, 2024
ISBN 978-5-0064-8466-5
Создано в интеллектуальной издательской системе Ridero
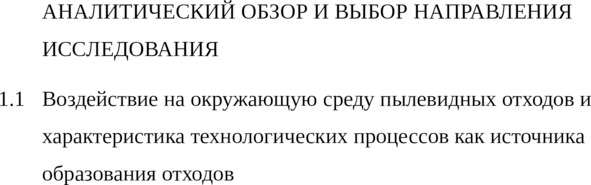
Значительная часть современных технологических процессов связана с изготовлением, переработкой, транспортированием и применением порошкообразных материалов, и сопровождается образованием большого количества пылевидных отходов. Недостаточное внимание к воздействию на окружающую среду пылевидных отходов, которые к тому же содержат ценные компоненты, несовершенство или высокая стоимость существующих систем разделения пылевидных отходов приводит к тому, что количество последних увеличивается. Неиспользуемые отходы производства в значительных количествах накапливаются в отвалах, что приводит к негативному воздействию на окружающую среду.
На территории России в отвалах накоплено около 80 млрд. т. различных твердых отходов [55, 103, 104, 106, 107, 114]. В связи с недостаточным количеством полигонов для складирования и захоронения промышленных отходов, широкое распространение получила практика размещения отходов в местах неорганизованного складирования (несанкционированные свалки), которые не отвечают действующим нормативам, представляя особую опасность для окружающей среды [30, 91, 108, 109]. Объемы размещения отходов на несанкционированных свалках, площади занятых под них земель постоянно растут, а, следовательно, растет и негативное воздействие на окружающую среду. Например, в Волгоградской области общая площадь только стихийных свалок превышает 400 тыс. кв. метров и складируется там более 100 тыс. т отходов [61]. А площадь санкционированных девяти полигонов промышленных отходов – около 210 га. Хранится на них приблизительно 50 млн. т. отходов и каждый год эта масса увеличивается еще на 2 млн. т. [61].
Положение с отходами производства выросло в огромную экологическую проблему, и необходимость ее решения обусловлена загрязнением окружающей среды и истощением природных ресурсов.
Технологические процессы производства строительных материалов сопровождаются образованием значительного количества пылевидных отходов, содержащих наряду с посторонними включениями, исходное сырье, которое может быть возвращено в производство. Извлечения посторонних включений позволяет, с одной стороны, снизить негативное воздействие отходов на окружающую среду, а с другой стороны обеспечить экономию минеральных природных ресурсов [68].

В Волгоградской области накоплено 1,657 млн. т. и ежегодно образуется 159 тыс. т. отходов производства щебня, содержащих щебень и глинистые частицы [114].
Сырьем для производства щебня (фракционного камня) служит горная масса. Добытый в карьере материал представляет собой смесь кусков различных размеров и формы. В горной массе находятся обычно различные примеси (ил, глина), содержание которых в товарном продукте недопустимо. Для того чтобы горную массу превратить в качественный материал, необходимо выполнить целый ряд технологических операций, основными из которых являются дробление и сортировка. [50].
По химическому составу породы состоят в основном из окиси кальция и окиси магния. Физико-механические свойства карбонатных пород характеризуются значительной неоднородностью. Плотность изменяется от 2,60 до 2,96 г/см3, объемная масса от 1,79 до 2,81 г/см3, пористость – от 35,5 до 1,1%, водопоглощение от 0,44 до 21,18%, прочность -от 31 до 1503 кгс/см2 в насыщенном водой состоянии. Коэффициент морозостойкости изменяется от 0,45 до 0,97. Эти данные [68] приведены для горной массы, добытой в карьере «Перекопский» Клетского района Волгоградской области
Технологический процесс производства щебня состоит в последовательном дроблении и сортировки. Дробильно-сортировочная установка состоит из следующих элементов: – питателя пластинчатого ТК-15А-01; агрегата крупного дробления СМ-16Д; грохота сортировки; агрегата передвижного среднего дробления СМД-131А; агрегата сортировки передвижного СМД —174 [50].
Установка оснащена металлоискателем, семью конвейерами ленточными ТК. Из карьера сырье доставляется автосамосвалами КРАЗ, КАМАЗ и ссыпается в приемный бункер установки, оттуда питателем подается на дробление. Продукт дробления подается на грохот сортировки, где происходит рассев на фракции 0¸10мм, 10¸20 мм; 20¸70мм. Фракции 0¸10мм, 10¸20 транспортируются на склад. Фракция 20¸70 мм поступает на агрегат среднего дробления СМД -131 А. На этом агрегате происходит дробление на фракции 20¸40 мм, 40¸70мм. Раздробленная порода подается на агрегат сортировки СМД-174. После сортировки фракции 20¸40 мм, 40¸70мм подаются на склад [35—37]. Схема производства щебня представлена на рис. 1.1. [35].
Отсевы карбонатной породы, образующиеся после грохочения, отбираются и отдаются в лабораторию на анализ на содержание пылеватых и глинистых частиц. Как правило, содержание пылеватых и глинистых частиц превышает 3% по массе, следовательно, такое сырье не пригодно для производства щебня [119—120] и направляется в отвал. Отсевы щебня складируются в карьерах, засоряя огромные территории, в то время, как отделение щебня от глинистых позволило сократить воздействие пылевидных отходов на окружающую среду, вернув их в производство.
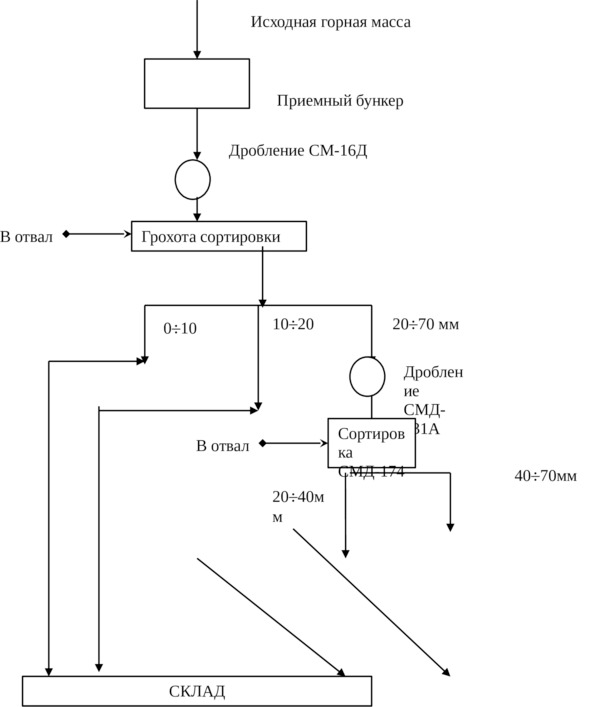
Рис. 1.1. Схема технологического процесса производства щебня [35].

В алюминиевом производстве на участке просева глиноземных сметок ежегодно образуется порядка 3750 т пылевидных отходов, содержащих ценное сырье —глинозем, наряду с посторонними включениями [45, 46]. Наличие посторонних включений препятствует их использованию в производстве, поэтому отходы направляются на полигон, что оказывает негативное воздействие на окружающую среду. Отделение глинозема от посторонних включений позволит сократить количество образующихся отходов за счет их частичного использования и снизить воздействие на окружающую среду, сохранив при этом ценные минеральные ресурсы.
В основе производства алюминия лежит электролиз криолито-глиноземных расплавов [9, 125]. Основным и самым дорогостоящим компонентом сырья является глинозем (Al2O3), который в России не производится и доставляется с Украины железнодорожным транспортом. Поэтому вопросы его рационального использования и возвращения в производство являются первоочередными.
Загрузка глинозема в электролизёр производится с помощью самоходных машин МРГ, МРС. Этот процесс сопровождается естественными потерями сырья [125]. Полы электролизного цеха снабжены решетками, для того чтобы просыпаемый глинозем собирался в специальном помещении нижнего уровня. Получаемый таким образом продукт, содержащий глинозем и 15% кремнезем с примесями, называют глиноземными сметками. Эта пылеглиноземная смесь собирается в мульды и транспортируется на участок просева глиноземных сметок, засыпается в бункер, оборудованный колосниковой решеткой [9, 1252]. Отделенная более мелкая фракция транспортером направляется на грохот. Просеянный продукт собирается в бункер. Глиноземные сметки, отделенные от крупных примесей, в настоящее время используют только в качестве насыпных подушек электролизеров. Однако, большая их часть сейчас направляется в отвал. Экономически целесообразно было бы часть данного продукта возвращать в электролитическое производство алюминия, однако это не допускается по ГОСТ 6912.1—93 из-за высокого содержания примесей [11]. Таким образом, ежегодно теряется значительное количество основного сырья производства первичного алюминия и возрастает техногенная нагрузка на окружающую среду. В связи с этим очень актуальной является проблема отделения глинозема от примесей.

Анализ технологических процессов позволил определить, что в производстве щебня и при просеве глиноземных сметок образуются пылевидные отходы, содержащие, наряду с исходным продуктом и посторонние включения, которые не позволяют их повторно использовать в производстве. Для снижения антропогенного воздействия на окружающую среду и сохранения минеральных ресурсов необходимо снизить количество образующихся пылевидных отходов посредством совершенствования системы их разделения.
В настоящее время для отделения твердых частиц применяются различные методы сепарации, в том числе магнитная, акустическая, электростатическая сепарация, разделение под действием гравитационных сил, центробежных сил, а также разделение по аэродинамическим свойствам пыли. В данной работе рассматриваются только сухие методы, поскольку применение мокрых методов сепарации делает невозможным или слишком сложным и дорогостоящим использование отделенных компонентов в производстве и промышленности строительных материалов.
Магнитная сепарация сыпучих материалов. Магнитные сепараторы – это многоцелевые системы, предназначенные для отделения магнитных примесей от немагнитных [59]. Различают магнитные сепараторы, использующие в своей работе постоянные магниты и электромагниты.
Магнитные сепараторы для сыпучих веществ обычно устанавливаются в трубопровод, по которому транспортируется сыпучий продукт. Сепараторы такого типа предназначены для удаления из сыпучих материалов случайно попавших железосодержащих примесей, при их небольших количествах. Магнитные системы генерируют неоднородное магнитное поле, которое отделяет и удерживает магнитные примеси на поверхности магнитных труб. Магнитный сепаратор необходимо периодически очищать от накопленных магнитных примесей. Это может производиться вручную, полуавтоматически и автоматически в зависимости от типа сепаратора.
В настоящее время используются следующие основные типы сепараторов на постоянных магнитах: барабанные сепараторы, плоские магнитные сепараторы, магнитные сепараторы из системы выдвижных решеток [59].
Существует большое разнообразие конструкций магнитных сепараторов [59]. Магнитный способ сепарации достигает большой эффективности в основном за счет интенсивной магнитной коагуляции, образуя агрегаты ферромагнитных частиц. Однако, во-первых, магнитная сепарация не позволяет разделять пылевидные отходы на фракции, а во-вторых, она применима только для отделения частиц, обладающих магнитными свойствами.
Сепарация в акустическом поле. В последние годы разделение пылегазовых потоков проводят с помощью акустических полей. Акустическая коагуляция осуществляется при воздействии на запыленный газ упругих колебаний звуковой и ультразвуковой частоты. Эти колебания вызывают вибрацию пыли, в результате чего растет число их столкновений. Процесс коагуляции происходит при силе звука не менее145—150 децибел и частоте 2—50кГц [53]. Скорость пылегазового потока не должна превышать при этом величины критической скорости, определяемой силами сцепления в данной неоднородной системе. Кроме того, концентрация дисперсной фазы должна быть в пределах 0,2—230 г/м3 [53]. Акустическая коагуляция находит промышленное применение для предварительной очистки горячих газовых потоков, а также при обработке газов в условиях повышенной опасности. Акустическая коагуляция также не позволяет классифицировать частицы по фракциям. Кроме того, этот метод применим для мелкодисперсной фракции.
Сепарация в электрическом поле. Сепарация в электрическом поле основана на том, что при поступлении пылевоздушной смеси в неоднородное электрическое поле в местах с большим напряжением образуются ионы, которые движутся в направлении осадительного электрода под воздействием сил поля [53, 126]. При движении эти ионы поглощаются частицами пыли, увеличивая их заряд. Заряженные частицы будут продолжать двигаться к осадительному электроду и оседать на нем. Учитывая, что частицы могут получать большие заряды, несмотря на малую массу, то и силы электрического поля намного больше инерционных и гравитационных. Но электрическая сепарация эффективна для частиц менее 10 мкм [53].